ALUMINIUM, A BRILLIANT STORY DESIGNED TO LAST
“What do you think of a metal as white as silver, as unalterable as gold, as easy to melt as copper, as hard as steel, malleable, ductile and brighter than glass?”
It was 1857 when Charles Dickens described the properties of aluminium in a century when the metal was considered more precious than gold. Twelve small ingots of aluminium had just been exhibited at the ‘Exposition Universelle’, an exhibition organised by Napoleon III, where the metal was presented as a precious rarity.
Parisian ladies, struck by its brilliance and lightness, immediately ordered jewellery such as pins and rings to show off.
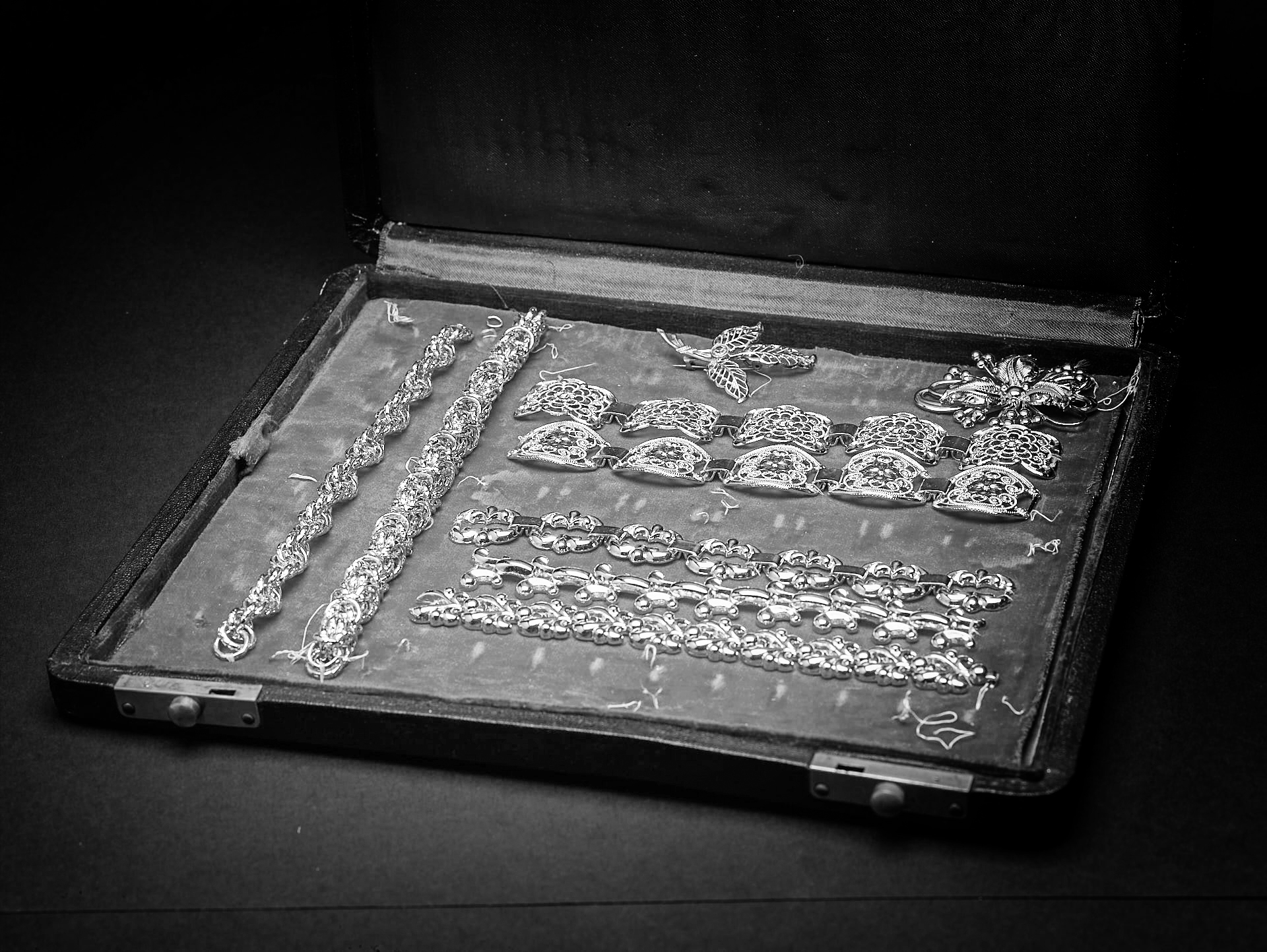
Napoleon III understood its potential for warfare and financed studies for the production of aluminium weapons and armours for the army.
However, the extraction process was so complicated and expensive that it was abandoned after producing only two helmets, which Napoleon melted down to create a personal set of aluminium cutlery.
It wasn’t until 1886 that we an industrial production process was conceived to allow large quantities to be produced at an acceptable cost. In that year, two scientists discovered the process of electrolytic melting of alumina, opening the doors to the large-scale production of aluminium and its many industrial applications.
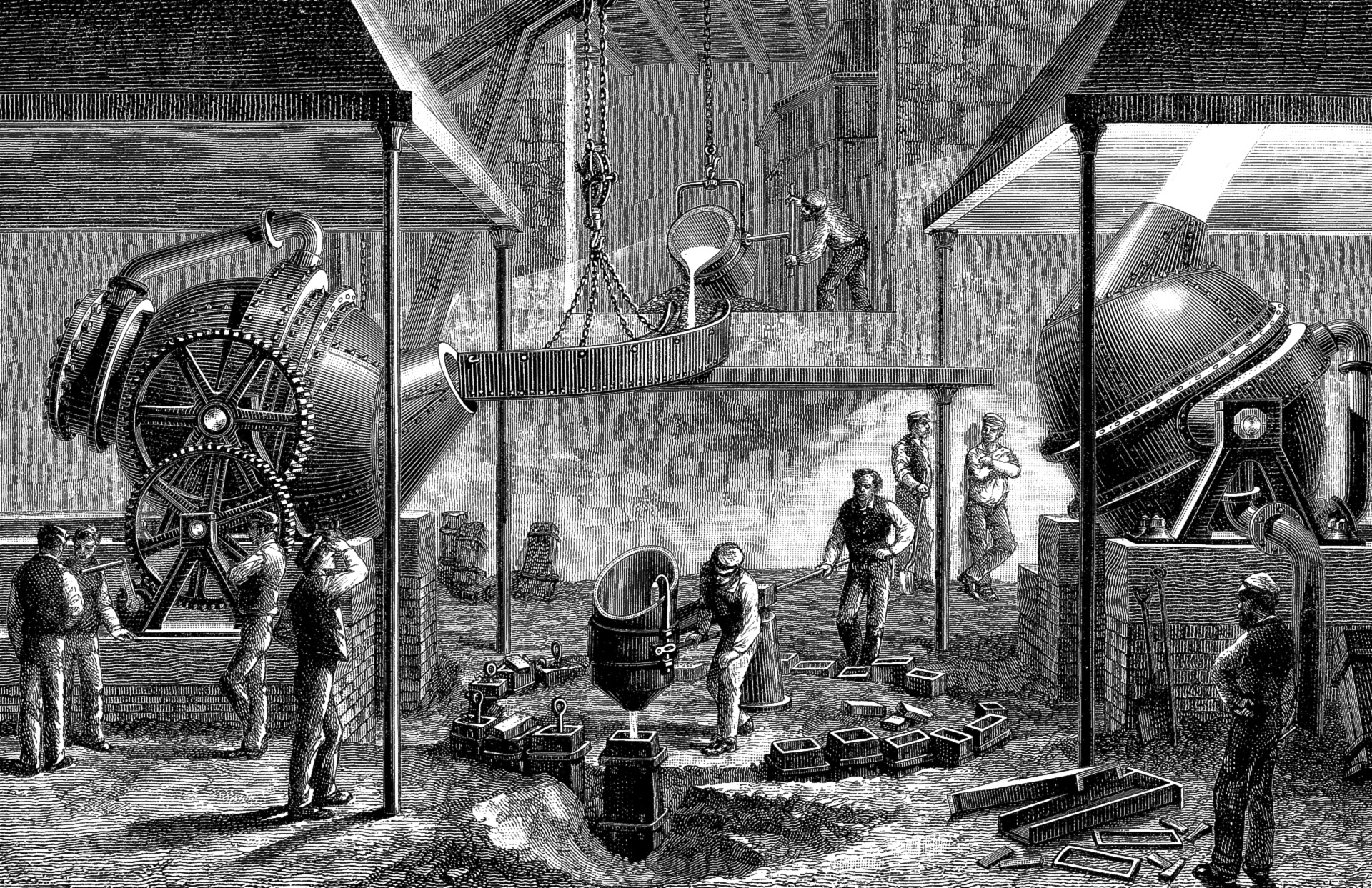
The potential of aluminium was immediately clear to two bicycle manufacturers, the Wright brothers, who used their experience with wheels to create the first flying machine. The main problem they faced was reducing the weight of the engine, brilliantly solved by using a block of aluminium. On 17th December 1903, the Wright Flyer took off to make its first 30-metre flight at an altitude of 3 metres.
Aluminium enabled man to realise his long-standing dream of flying.
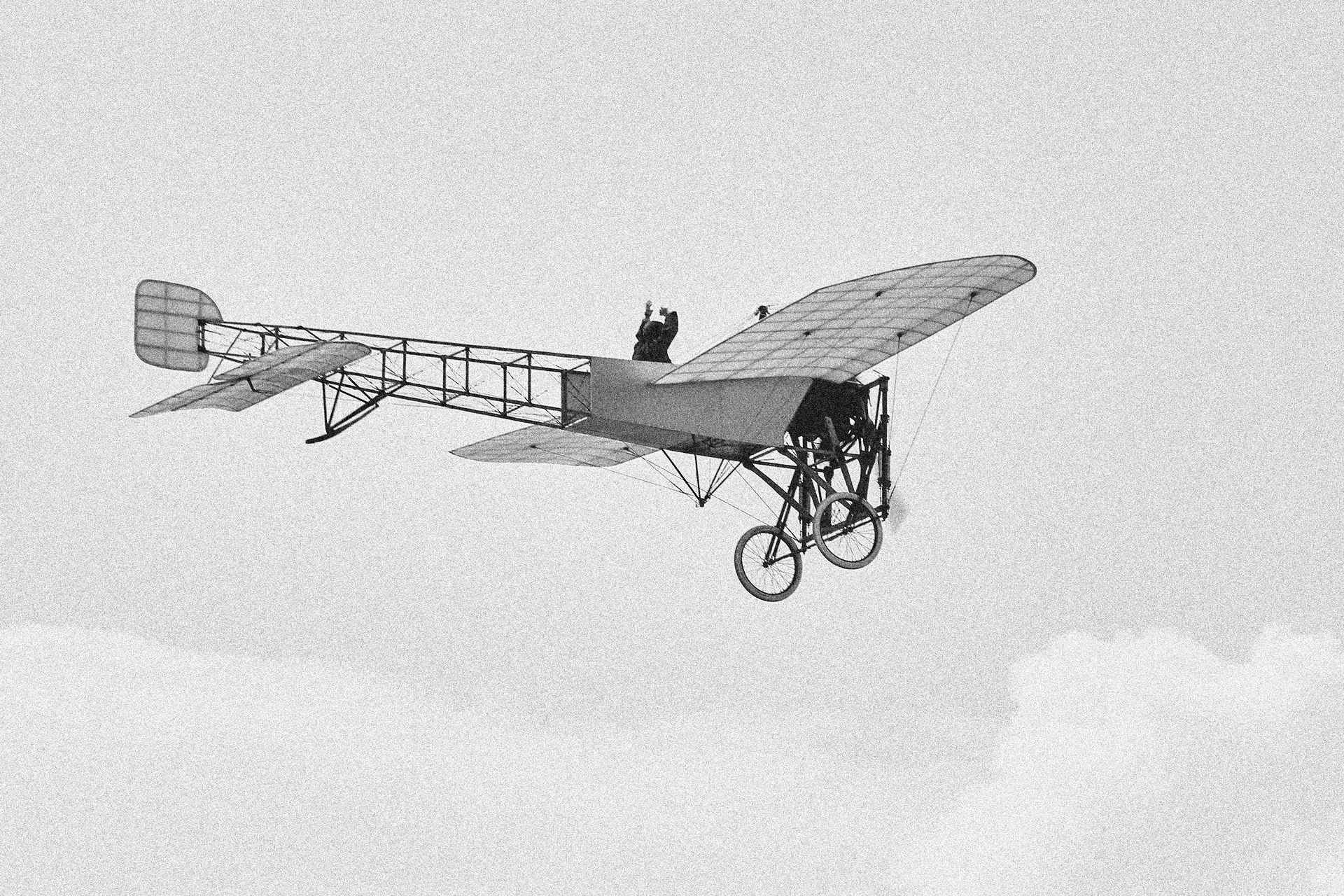
Since then, the industrial applications of aluminium have multiplied in all sectors and the metal has become part of our everyday life, inspiring some experts to defineour era as the Age of Aluminium.
Cars, planes, motorbikes, industrial production machines, taps, pumps, accumulators, electric motors, aerials, lamps, televisions, remote controls, telephones, wardrobes, kitchen accessories, coffee makers, irons, beds, pens, door and window frames, heating systems, sporting equipment, bicycles, toys….
The aluminium industry is focusing on improving plants technology and production performance to make the production process simpler and cheaper. In fact, the extraction of bauxite, a rocky clay coloured in shades of pink, red and grey, and its subsequent transformation into alumina and the electrolytic extraction converge into an “energy-intensive” industrial process: to produce 1 ton of aluminium, indeed, 4 tons of bauxite and 14,000 kWh of energy are needed.
In one year, around 100 million tonnes of bauxite are extracted worldwide for the production of the primary aluminium.
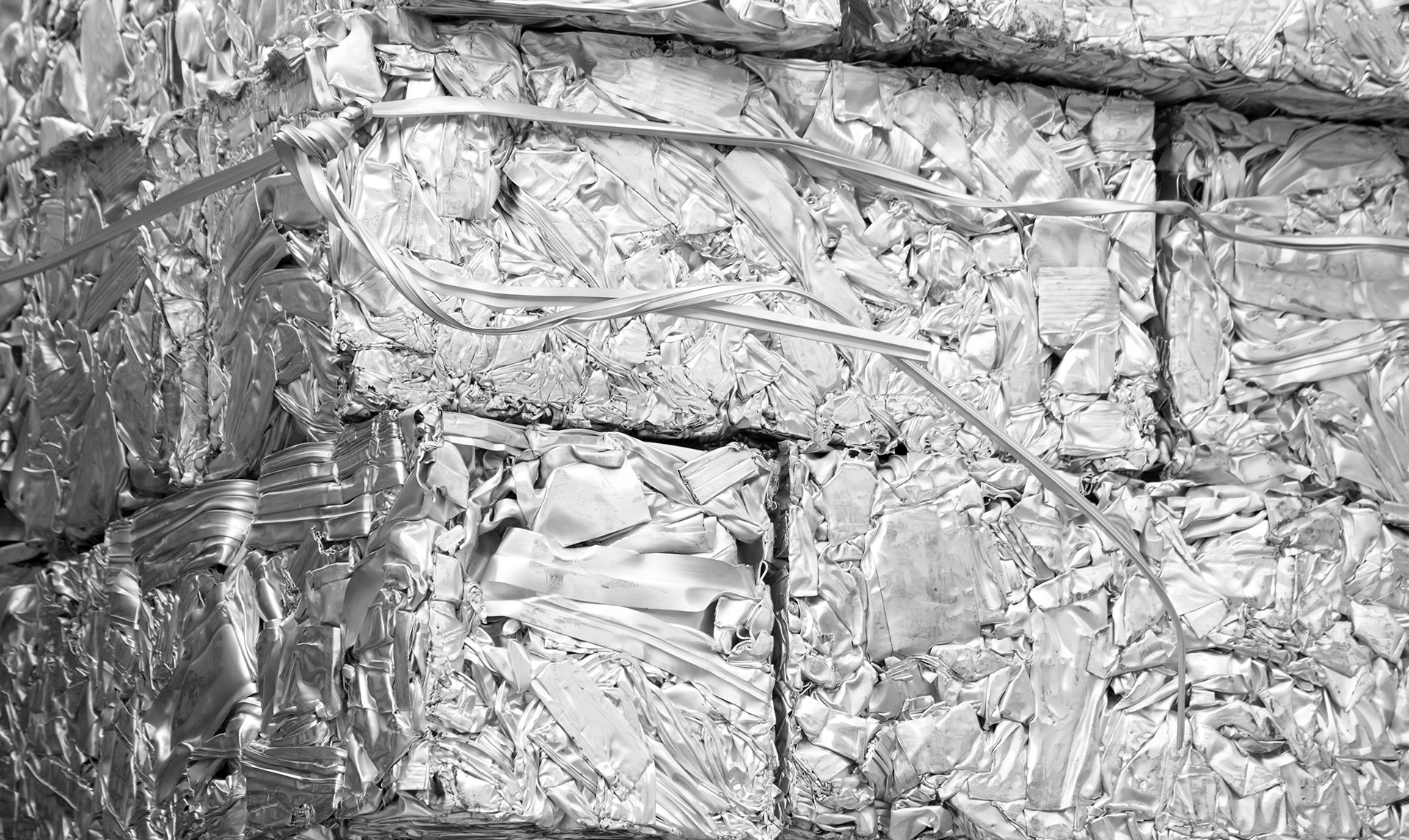
The aluminium production industry is taking up the challenge of the future by focusing on the recycling process for the production of the secondary aluminium. Thanks to this metal’s properties, aluminium can be re-melted to secure endless new lives, in a process that consumes 95% energy less and emits less than half of CO2 into the atmosphere.
After having impressed emperors and governments, having revolutionized the industrial history contributing to the success of the first aircraft, aluminium is now the new candidate for the Green Revolution.
For more information